以空压机为代表的动力中心是很多工业企业非常重要的组成部分,也是企业能耗管理重点所在。正是因其特殊性和代表性,动力中心的“智能化“升级,已被看作是传统制造企业拥抱工业互联网,进行产业升级转型的第一步和最佳“切入点”。
某钢板制造企业位于中国北方的彩涂钢板集散地山东省,是集建筑钢品设计、生产、贸易、科研于一体的大型民营集团化企业。主营业务包括:聚氨酯板,聚氨酯保温板,聚氨酯复合板、净化板、医疗洁净板、洁净板材、彩钢板、岩棉净化板等保温材料。
空压机是该企业工厂生产动力主要来源,AOA体育·(中国)官方网站以“智慧气站”解决方案,根据企业现场实际情况,针对空压机无效耗电问题进行改造。

“智慧气站”解决方案的核心产品是AOA体育·(中国)官方网站自主研发的方略柜(Rolacab)。方略柜是智慧工业核心引擎MixIOT的机柜部署形式,集成了通讯、采集、计算、控制、存储等功能。方略柜部署在气站现场,使用AOA体育·(中国)官方网站的工业网关适配器Aprus采集空压机的控制器与电能表、管道的积算仪,用气末端的压力变送器等设备运行参数,再使用网线、Wifi或4G等方式,把采集到的运行参数上报到部署在方略柜中的MixIOT平台,通过MixIOT的动态配载(Dynaload)功能运用科学的算法计算最优空压机组配载策略,控制空压机运行状态。MixIOT对气站设备状态进行呈现、监控、统计、存储、预警,通过大数据分析,对空压机组优化策略进行更合理的调整和优化,也可以提供标准的数据开放接口,用于开发各种应用。还可以根据客户的选择,通过路由器将MixIOT平台处理后的数据上报到云平台,使用电脑、手机app对智慧气站进行远程管理空压机运行状态。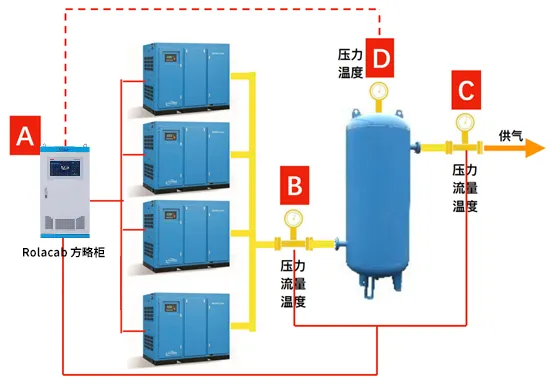
视不同客户的项目现场情况及复杂程度,一般情况下,“智慧气站”解决方案一个月内可完成实施交付。
客户工厂主要有4个厂房,每个厂房独立使用一台变频空压机,一线、二线、三线厂房之间管道是互通的,厂房与厂房之间的管道中间装有阀门,为常闭状态。四线厂房完全独立,因此,四个厂房可以默认为是相互独立用气。空压机产生压缩空气主要用于两部分:
1、车间生产用气,提供车间设备用气,气压需保持在0.75Mpa左右。2、给制氮机供气,生产出氮气供黑料罐和戊烷罐使用,末端气压基本只需保持在0.2Mpa以上即可。每个车间气站主要由1台空压机+2个储气罐+1根生产用气管道+1根制氮用气管道组成,具体情况如下:
5、用气末端压力:分为生产用气和氮气,生产用气直接使用压缩空气;氮气是将压缩空气经过制氮机后分离出用于黑料罐和戊烷罐。Ø一线,直接读取两个黑料罐压力;
Ø二线,增加压力变送器,读取戊烷罐末端压力。
Ø三线,直接读取三个黑料罐压力,增加压力变送器,读取戊烷罐末端压力。
Ø四线,增加压力变送器,读取黑料罐和戊烷罐共用主管道末端压力。
使用压缩空气的主要生产设备:
1、双带机、带锯机、码垛机、凉床,生产时开机,停产时关机。2、戊烷罐、黑料罐,生产时开机,停产时需保证罐内压力不处于负压状态,因此需实时监控进行补充压缩空气。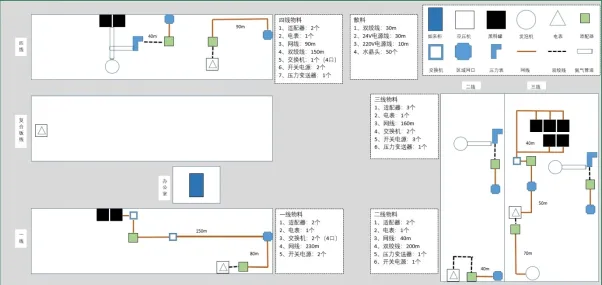
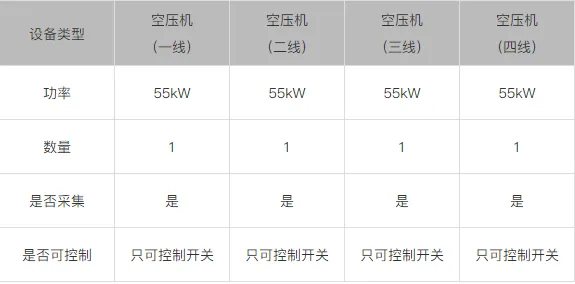
上述空压机都是变频空压机,给各个车间提供生产用气和氮气原料输入,车间不生产时,生产用气可关闭,但氮气末端压力,即使不生产时也需要保证末端压力正常。因此,车间空压机需保持24H开启,用于保证氮气末端压力正常,停产状态下,黑料罐和戊烷罐消耗氮气极少。车间7:50-19:00属于上班时间,夜间不生产;并且车间换线时间较长(大约1-2小时),以及白天不生产的情况。这些情况下,一直将空压机保持开启状态存在很大的能耗浪费。因此,实时监控氮气末端压力,压力正常时关闭空压机,接近异常时,开启空压机,对于节能降耗有很大的帮助。
上图为项目实施前一线空压机10天电量消耗和运行情况,可以很明显地看出空压机24小时都处于开机运行状态,即使夜间停产,为保证黑料罐、戊烷罐压力正常,空压机仍然开启着,并且一直处于加载状态,每小时大约有33 kW·h的电量损耗。另外,从上图还可以看出,白天生产时也有较多的时间处于换线或者停产状态,但空压机也是开启着,并一直处于加载状态,造成电量的浪费。根据现场了解到,停产或换线时,基本只需要保证黑料罐、戊烷罐压力正常即可,生产不需要用气,而黑料罐和戊烷罐在停产状态下用气量极少,只需偶尔补充氮气罐气体即可,但因为无法实时把控黑料罐和戊烷罐末端压力,为保证安全和后续正常生产,所以只能一直将空压机开启,保证充足供气。另外换线或停产状态下,产线没有关闭生产用气阀门的习惯,导致压缩空气一直经过生产管道被排放,因此,管道压力一直无法达到卸载压力要求,空压机一直处于加载状态。 通常情况下,造成气站有效利用率较低的原因一般分为以下四种:1、空压机本身配置调参原因;
2、设备维护不到位,或维保不及时导致;
3、设备、管道规划不合理,及管道密封不好,有漏气发生;
4、生产现场用气与气站机房人员无法实时确认现场用气,以至供需不平衡导致。
根据现场情况和客观条件限制,本次项目主要针对第四种原因制定具体解决方案。
通过上述分析,要优化当前气站有效利用率,主要需解决一个方面的问题,即供需不平衡导致的浪费问题。增加系统自动控制功能,实时监控每个气站黑料罐、戊烷罐的末端压力,当产线停产时,自动关闭空压机,当监控到黑料罐、戊烷罐的末端压力接近最低值时,系统自动开启空压机,及时补充末端氮气,保证末端压力正常。
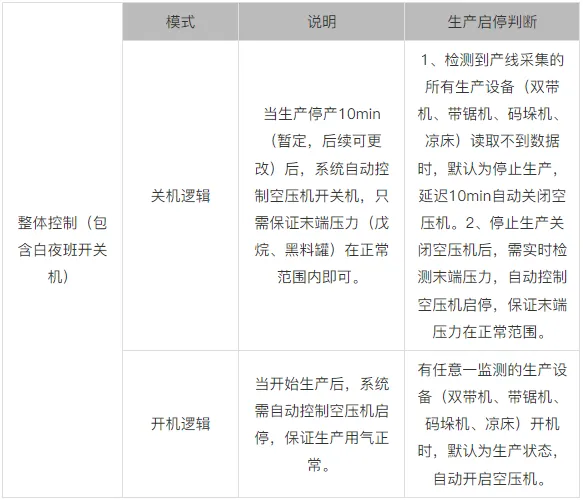
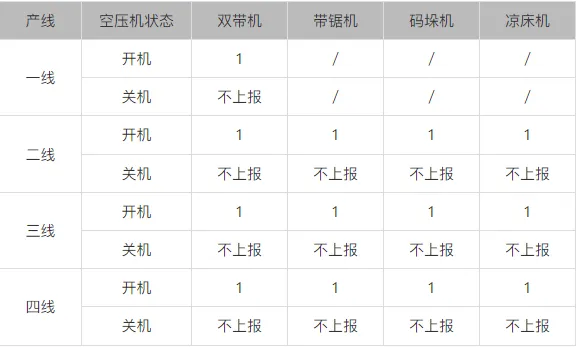
氮气末端所需压力如下:
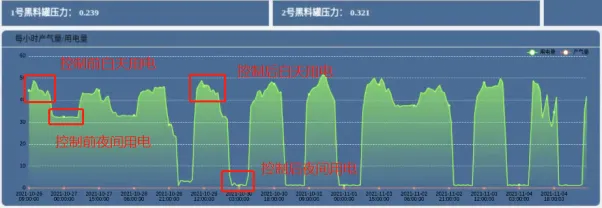
控制前,空压机夜间每小时耗电大约33kW·h,控制后,空压机夜间每小时耗电大约2 kW·h左右。大约平均每小时减少30 kW·h的耗电。一般夜间停产时间大约为10-12个小时,取平均值11小时。因此,一台空压机一晚可节约用电30×11=330 kW·h,一台空压机一个月仅夜间可节约电量近10000 kW·h。
上图是一线空压机状态和氮气末端压力曲线图,系统根据夜间氮气末端压力,自动对空压机进行开关机控制,保证氮气末端压力保持在正常范围。
通过系统的自动控制,大大减少了空压机的运行时间,有效的保证了氮气末端压力的正常,在安全和节能上达到统一。
二、三、四线节能前与一线情况一样,将自动控制扩展至二、三、四线后,停产状态下的节能效果也有了较大的提升,解决了空压机在停产状态下依旧要持续运行来保证氮气末端压力正常的问题,通过实时监测和自动控制,做到了既保证氮气末端压力正常,且减少空压机无效做功的问题。以下为其他三条线节能后的效果曲线图。
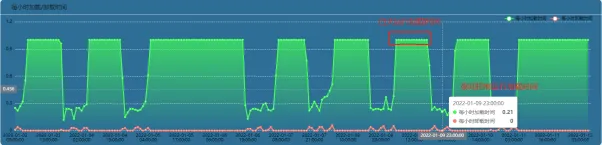
▲ 二线空压机增加自动控制后用电和运行时长
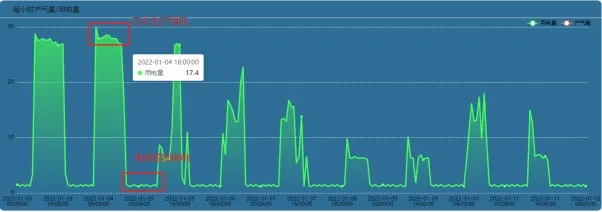
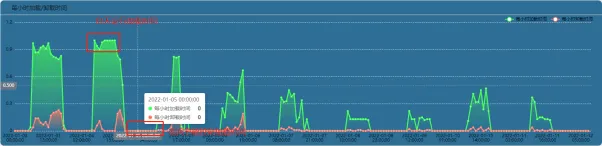
▲ 三线空压机增加自动控制后用电和运行时长
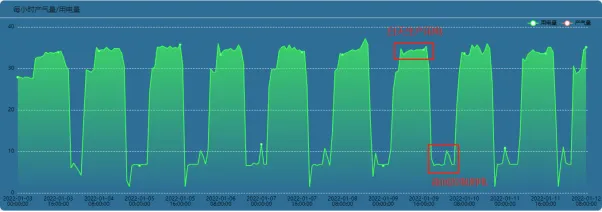
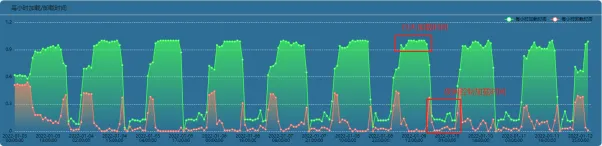
▲ 四线空压机增加自动控制后用电和运行时长
本项目未实施前,每台空压机日耗电量大约在1000kW·h,即4台空压机月耗电约120000kW·h。项目实施后,每台空压机每日大约可节电330kW·h,即4台空压机月节电可达40000kW·h,节电率约30%。